Unifying data for a seamless customer experience
JEOL sought a centralized solution to effectively manage product data and distribute it across all channels. The new system needed to support several key requirements:
Key objectives included:
- Transparent management of data from onboarding to publication.
- Distribution of accurate, relevant, and consistent information to eCommerce sites and electronic catalogs to enhance customer satisfaction.
- Integration of Product Information Management (PIM) and Digital Asset Management (DAM) into the existing system landscape.
- Enablement of batch updates for approximately 40,000 items to significantly improve operational efficiency.
- Quick, one-click search for the latest information on each product.
- Management of collected parts information in line with the ERP, including sales prices, image files, and text descriptions.
- Easy and secure access to product information for employees and partners.
Choosing Contentserv as the foundation for their product information management, JEOL partnered with Exa for project implementation. The solution’s comprehensive functions, flexibility, and scalability were pivotal in their decision. Centralizing previously scattered information was essential for improving operations and reducing manual efforts.
The project commenced in January 2020, experiencing some delays due to the pandemic. However, progress was made when Exa began the construction phase in November. They addressed technical challenges related to centralizing dispersed product information and integrating it with eCommerce sites. Contentserv became the core of JEOL's new after-sales service system, enriching data from the ERP system, centralizing technical information, and distributing it across eCommerce and service platforms.
One of the project's most significant challenges was developing an effective data model, which required continuous reviews and adjustments in conjunction with related systems like the call center and CMS. Contentserv’s advanced data tools were invaluable during this process. The dashboard helped identify missing data elements, and enriched content supported eCommerce operations. Robust workflow capabilities allowed JEOL to pinpoint critical data issues, prioritize solutions, and eliminate manual maintenance tasks.
About EXA
Exa Corporation is an IT services provider affiliated with JFE Steel and under the parent company Kyndryl Japan.
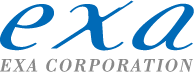
Leveraging cutting-edge technologies, EXA drives the evolution of Digital Transformation (DX), offering comprehensive services from system consulting to development, implementation, and operational maintenance, as well as advanced technologies such as cloud cognitive analytics and IoT:
https://www.exa-corp.co.jp/